With the highest Precision and unrivalled Evenness: Electroless Nickel
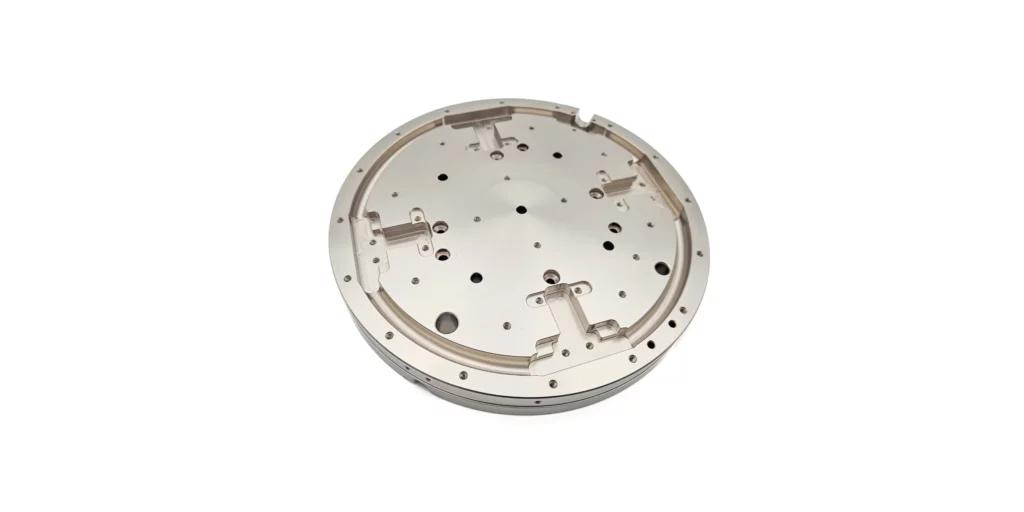
Electroless nickel surface coatings offer a whole range of important advantages for technically demanding components and fulfil requirements that are hardly achievable with other processes, such as high corrosion protection and high hardness and wear resistance.
Electroless nickel with possible layer thicknesses between 8 and 50 µm is particularly suitable for technical components that are subject to high stress. Especially for workpieces with complex geometric shapes and high demands on corrosion and wear protection, nickel plating in an external currentless nickel-phosphorus bath is the best choice: Extremely precise and with uniform coating thickness for almost all metals. All recesses or even bores are coated absolutely uniformly.
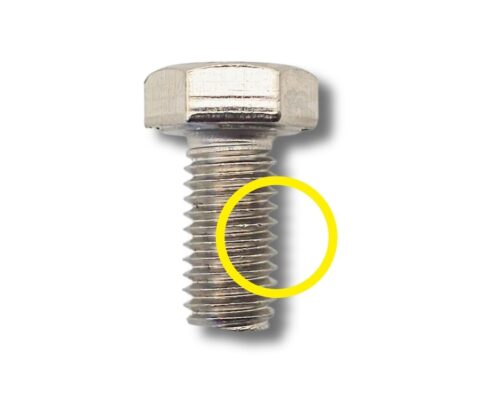
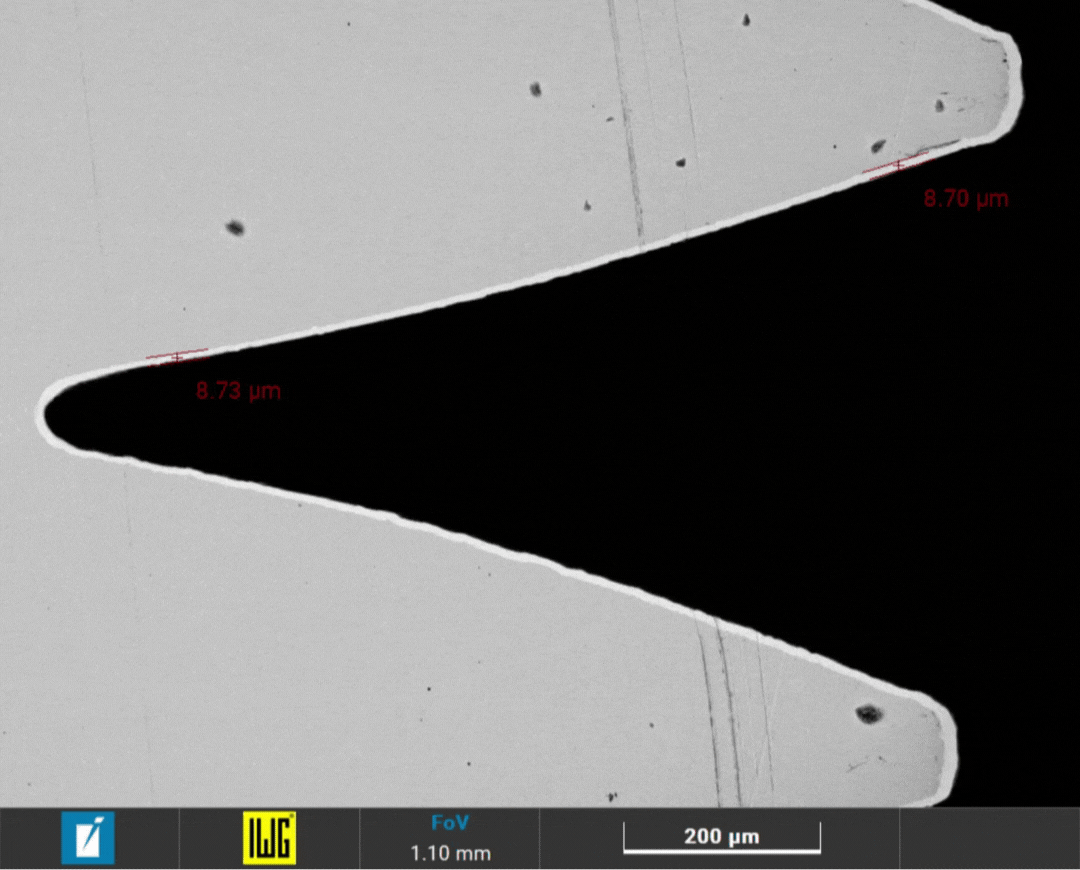
We have tested for you!
The electroless nickel plated screw (in the picture on the left) was cut in longitudinal section and analysed in our in-house analysis park using our Tescan Amber X FIB-SEM electron microscope. In the macro image on the right, the absolutely uniform Nidega® electroless nickel layer is very clearly visible.
Electroless Nickel Process: All Advantages at a Glance
- Perfect for functional applications
- Absolutely even and uniform coating
- Excellent corrosion protection
- High wear resistance
- Excellent hardness
- Solderable and weldable
- Magnetic or non-magnetic (depending on phosphorus content)
- Attractive appearance
- Optimum sliding behaviour
Our chemical Nickel Nidega® chem Processes in Comparison
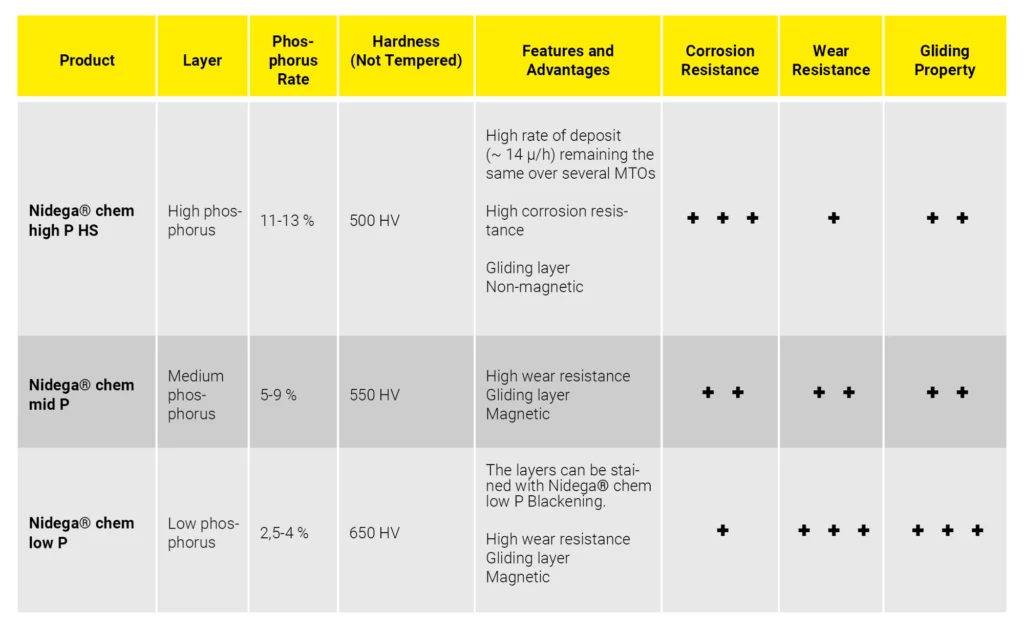