Our Plating Shop
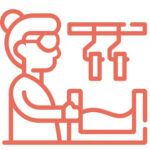
As part of our fully automated plating shop, we offer
Our Plating Services at a Glance
Our Plating Baths
We know our baths inside out because we use chemicals developed exclusively in our laboratories. These chemicals are analyzed and optimized continuously in our cutting-edge analysis park.
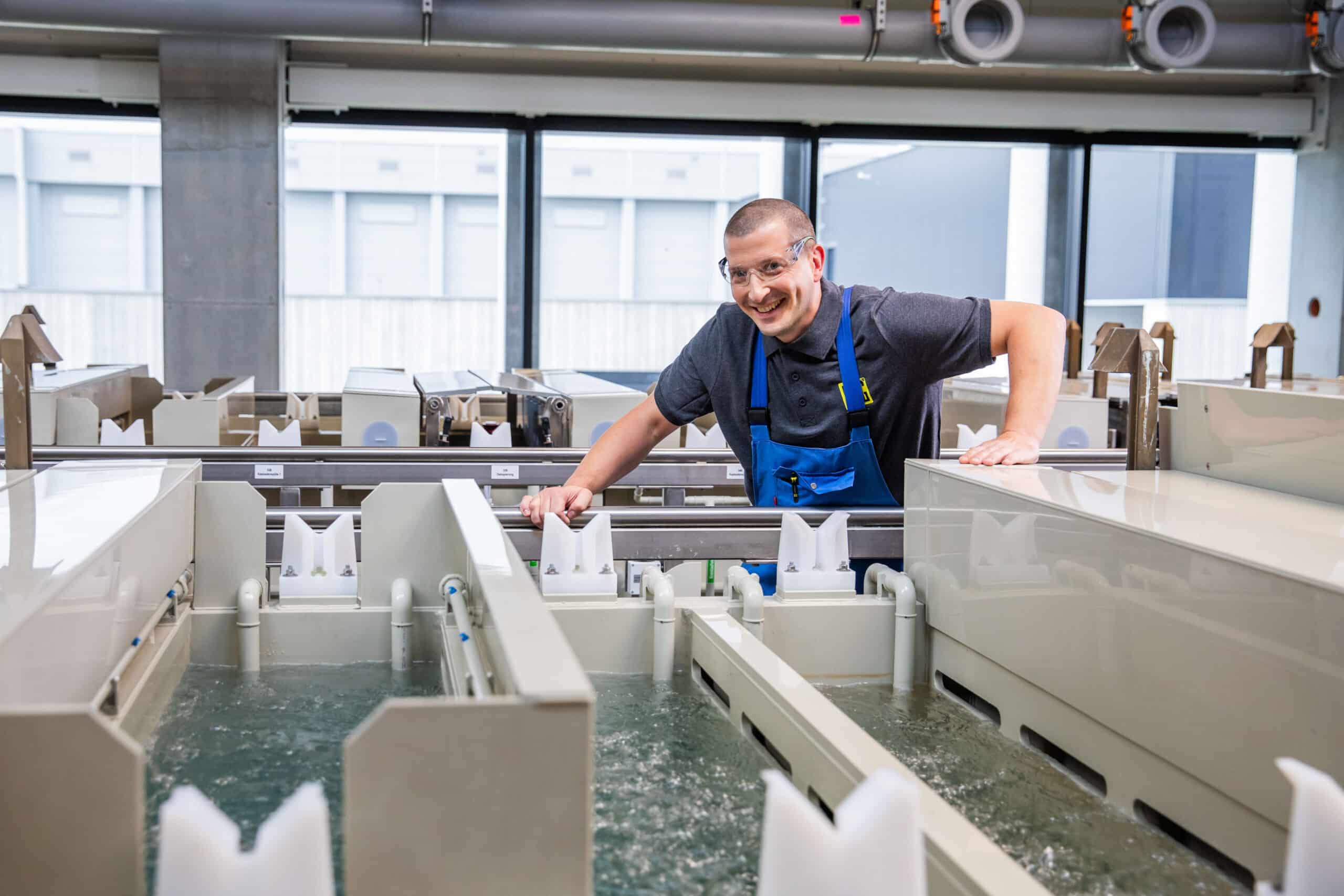
Pretreatment:
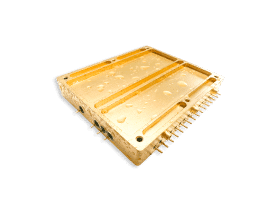
Non-precious metals & Chemical nickel
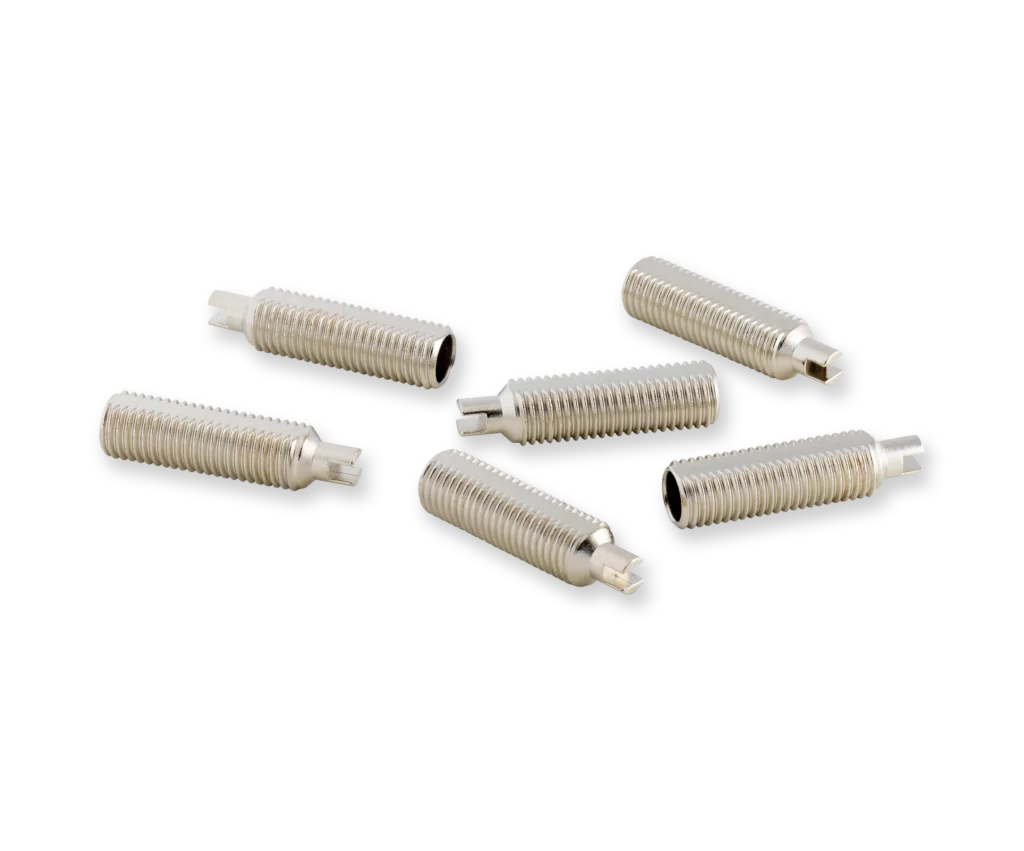
Precious-Metal Process Baths:
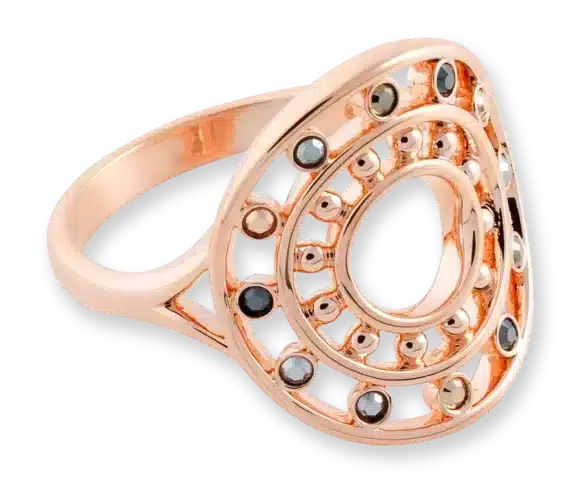
Posttreatment:
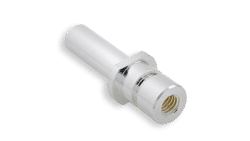
Our Goal is the Perfect Surface.
Quality control starts before plating begins here at IWG. All parts sent to us are received by our racking team at the plating line unit. Our highly trained staff check the parts for potential visible defects under perfect light conditions — by the way, the amount of daylight and resulting perfect light conditions were an intrinsic part of the planning phase for our racking unit. Once the parts have passed the visual check, the base material of the parts is analyzed in our laboratory using X-ray fluorescence to determine the best process for your products and their special needs.
Ready for the bath!
The parts are mounted on the racks by our staff by hand and then sent off to the plating line.
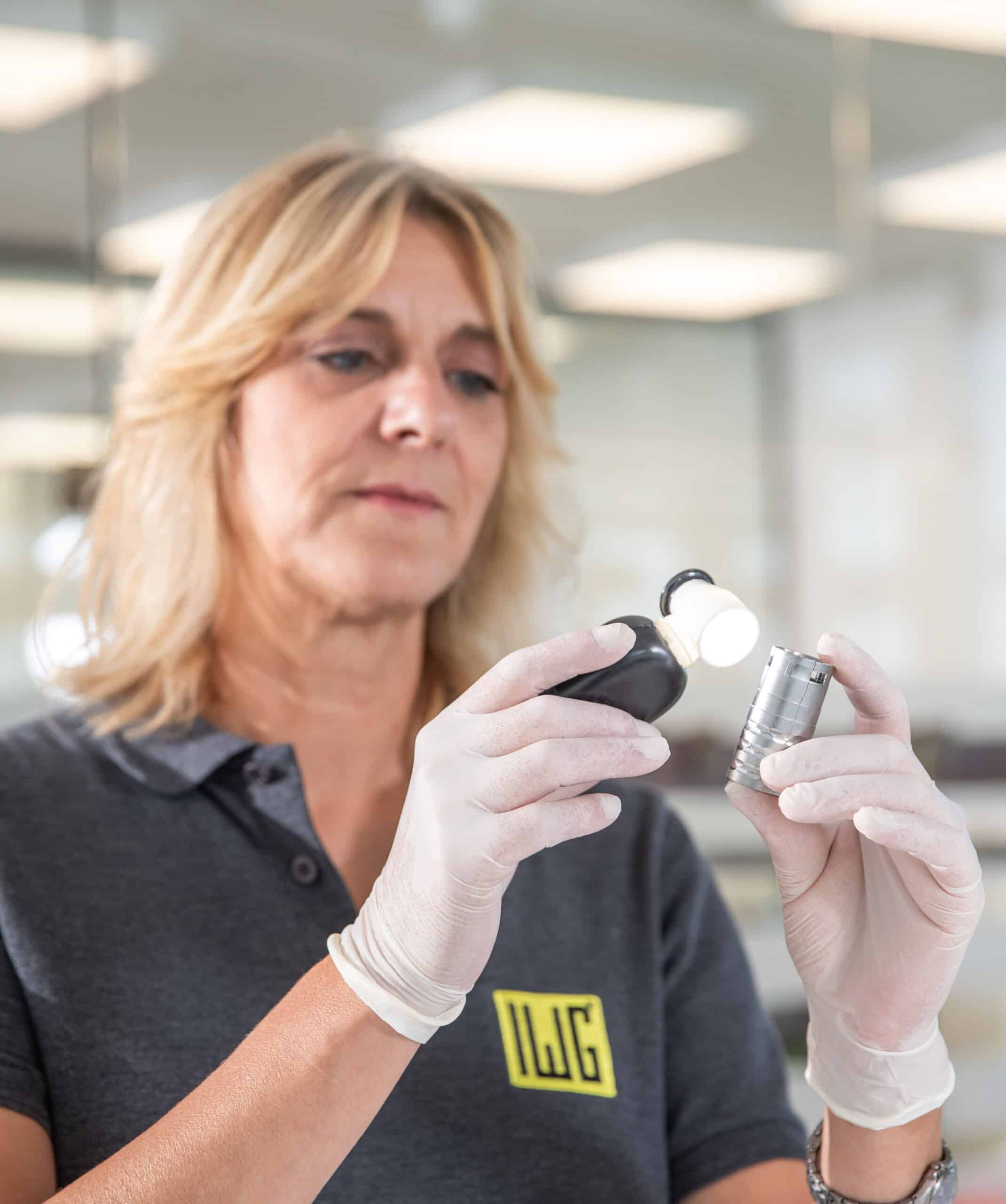
Plating Shop 4.0 – Plating Control
The entire process is controlled automatically. Each individual step is stored in the system, and the entire plating sequence is carried out automatically after the process has started.
Integration into our ERP system and the incorporation of all analysis parameters provided by the laboratory help us produce a digital twin that allows full traceability and 100% quality assurance.
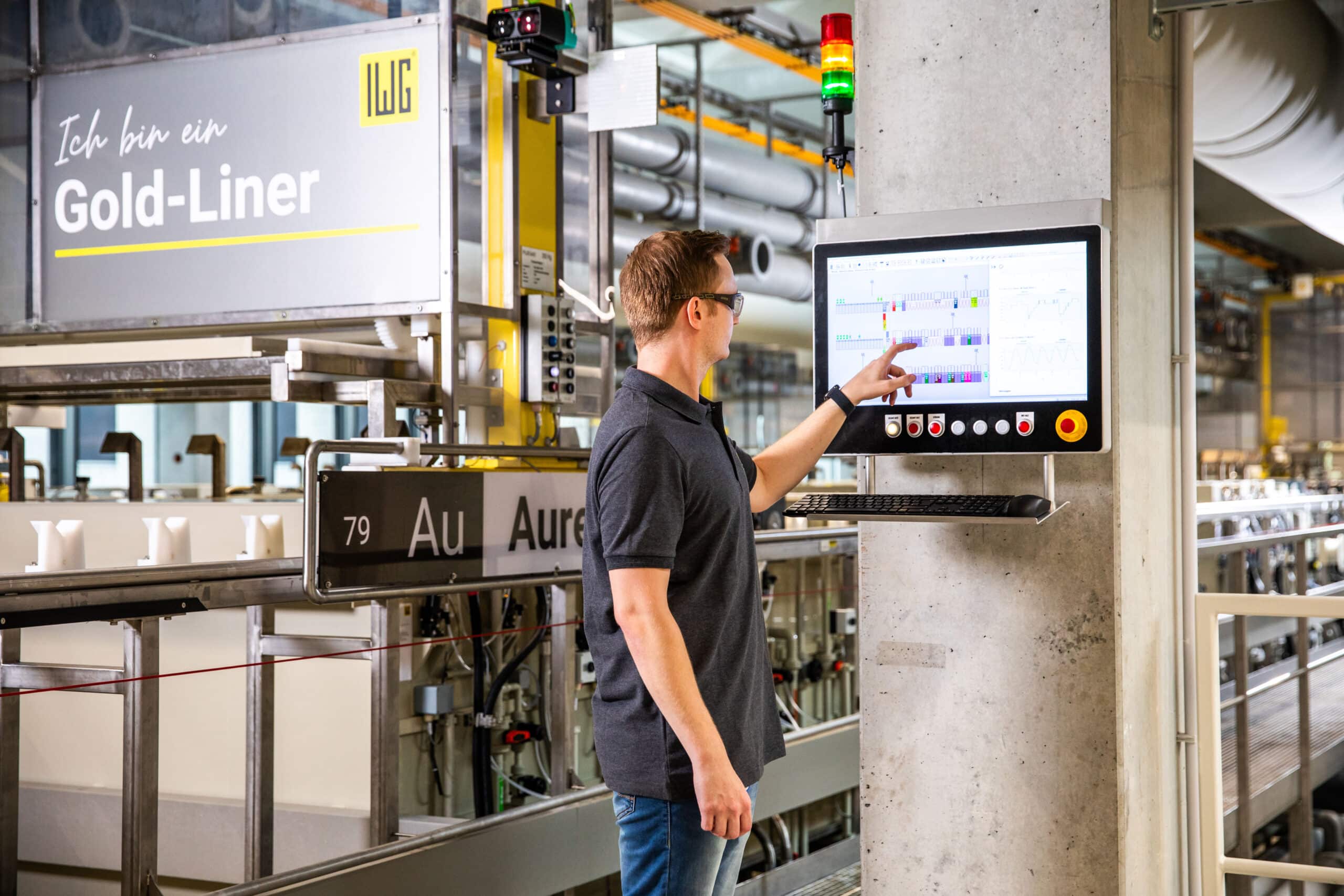
Effective Rinsing and Drying. For Flawless Results.
Perfect, stainfree surfaces can only be achieved by using clean water. This means the parts undergo two rinses at the end of each production process, during which we filter the water continuously using resin, thus reaching a conductivity of less than 1 µS (microsiemens). Surfaces are dried up to 50% faster than in conventional processing thanks to our condensation dryer! This is both surface and environmentally friendly!
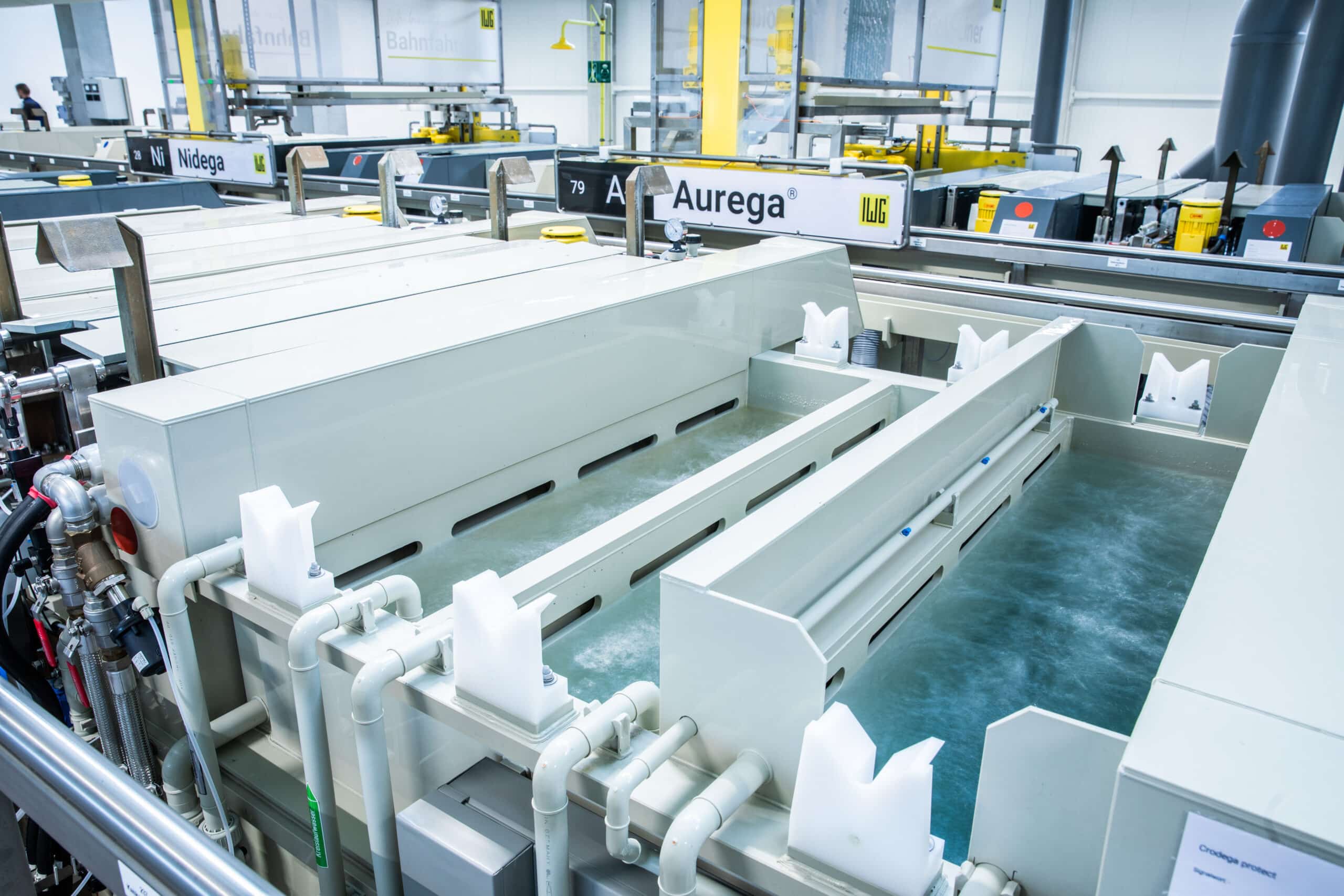
Final Inspections – Only Perfect Is Good Enough.
Once processing has finished, the dry, plated parts are taken off the racks. Samples are taken from each batch and given a thorough quality check. First, our staff check the plated surfaces for visual flaws under a microscope, and then they test the coating adhesion via bending, squeezing or cross cutting. The layer thickness is measured with our X-ray fluorescence equipment. The samples are then stored at our site as reference samples.
Safe Journey!
Your finished, tested parts are packaged carefully on-site and delivered back to you.
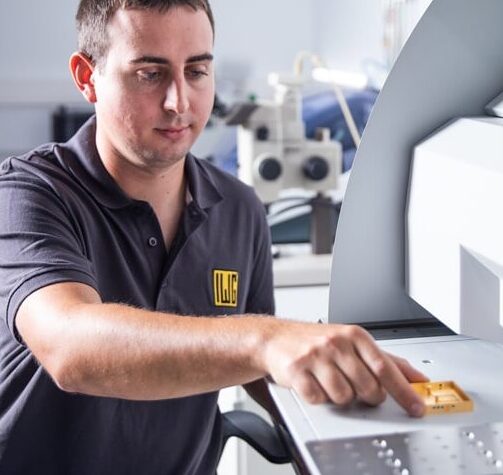
Cost-Efficient for Our Customers.
Our In-House Precious Metal Recovery.
We know that raw materials are scarce and valuable. Therefore, recovering precious metals is a key focus for our plating services. Precious metals are recovered from rinse water via an electrolysis process and put back into our baths to be recycled. This saves both natural resources and — most importantly — your money!
We monitor all processes in our in-house laboratory and analyse our rinse water. Any discrepancies can be identified immediately. Not only do we offer you the equipment and analysis services you need but we can support you with our know-how for all plating issues.
The recovery of precious metals is one of our core competences. Find out more about our recycling services for your own baths here.
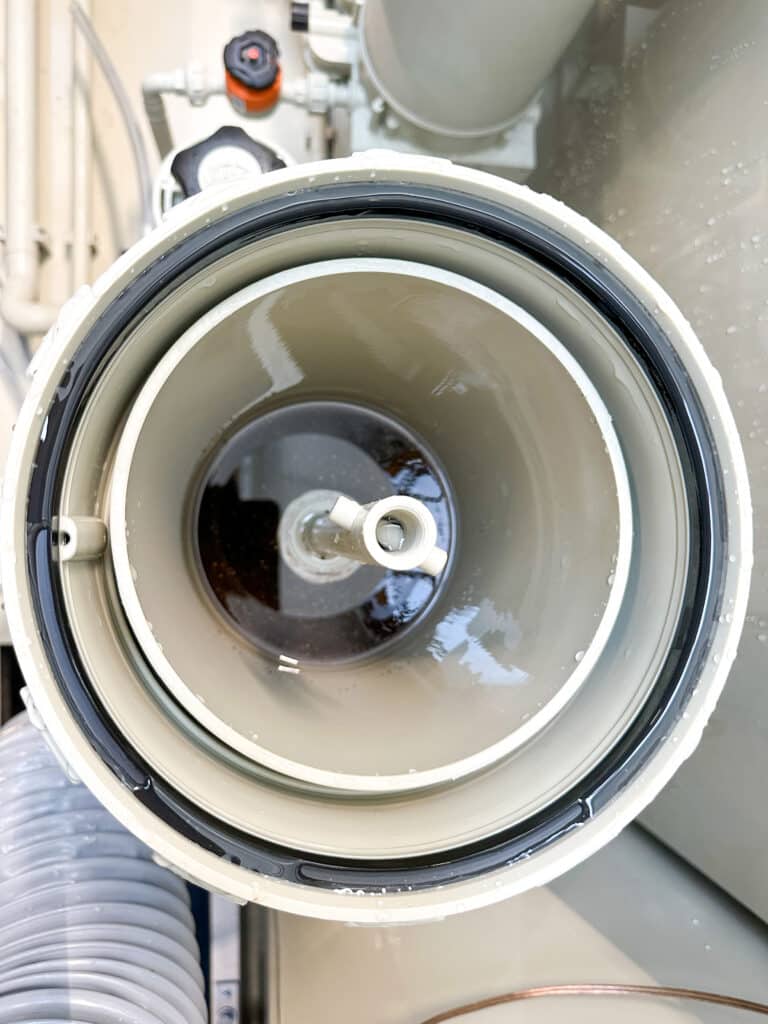
Our Experimental Plating
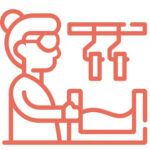
Our experimental plating service help us prepare newly developed baths with a volume of up to 120 liters for simulations under real test conditions. We can also offer small-scale series sampling and production for parts used in jewelry and technical equipment.
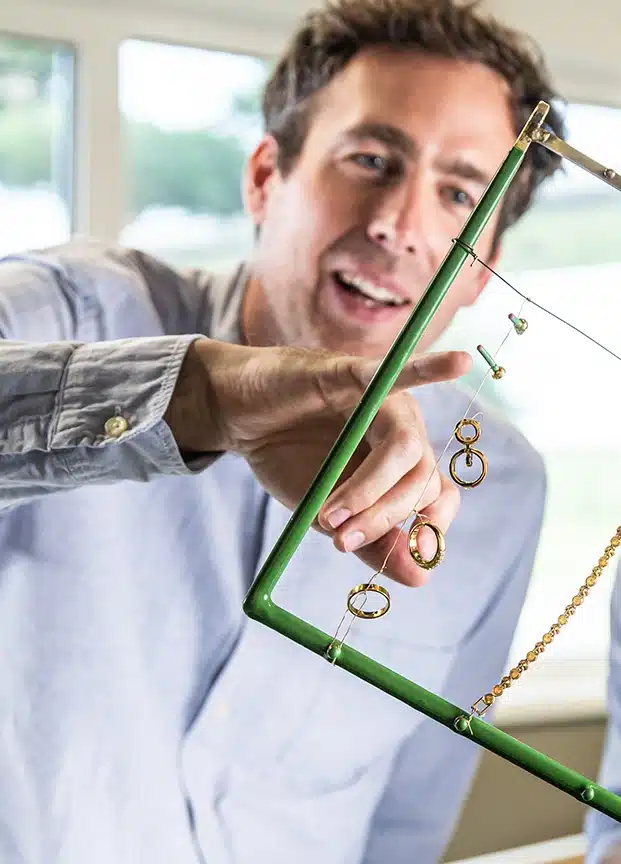
Galvano Full-Service –
Bringing Everything Together.
We have combined our three service fields Chemicals, Lab Solutions and Plating Service into the GALVANO COMPETENCE CENTER to offer you a complete electroplating spectrum.
Your advantage with IWG as a full-service provider: we use the chemicals developed in our laboratories in our fully automated production plant. As a result, the baths can be adapted to your individual needs and optimized continuously. All core processes are automated and can be tracked continually. We can meet almost all customer demands and have a suitable process for you — whether for chemical nickel plating of aluminum parts, precious metals, such as silver and palladium, or alloys with rhodium in rack and barrel plating.
Our Galvano Competence Center at a Glance
State-of-the-Art Technology at IWG –
for Our Environment
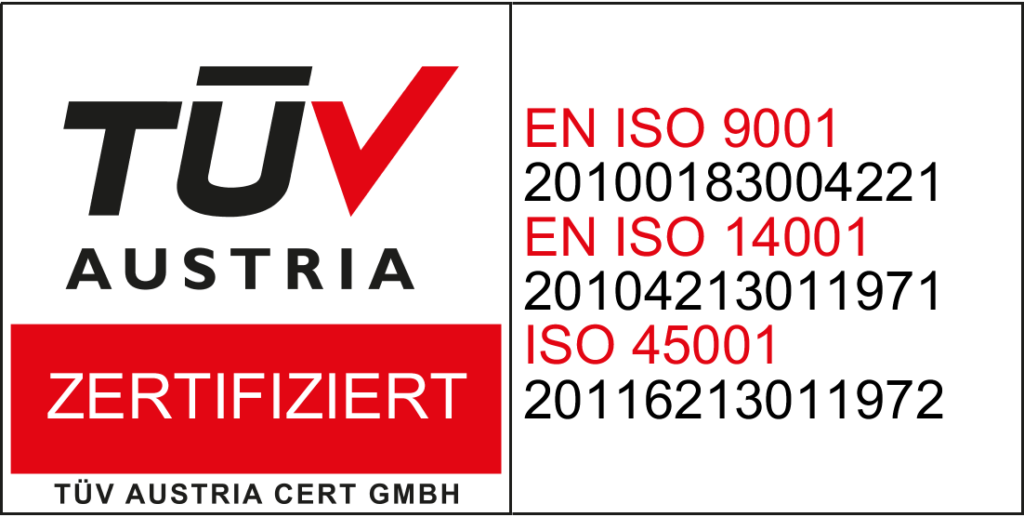
Sustainable chemicals management is not just value added and economical — it is also resource and environmentally friendly.
We have committed ourselves to using our resources more efficiently — i.e., recycling and reusing and keeping waste to a minimum, so that long-lasting, high-quality substances are not released into the environment.
PV-Plants
Not only do we use energy efficiently and effectively, but we also generate most of our power ourselves. Our photovoltaic system generates up to 240 kW of electricity, turning our plant into a genuine Green Building.
Building and Bath Heating
Both our main building and our baths are heated using air-water heat pumps.
The air-water heat pumps generate heat for one water cycle of bath heating using heating coils. This saves electrical energy and reduces the fire hazards encountered when using dry-running, plastic baths.
Water Cycle – Wastewater
We found we needed to build a wastewater treatment facility for both ecological and economic reasons. Precious metals are recovered as purely as technically possible and put into our recycling process. The wastewater is treated once the precious metals have been separated from the baths and rinse water. The method used and capacity level depends on the baths involved. Given the varying composition of the baths and varying natures of the hazardous substances in them, there are different substance flows requiring a range of different treatments. The catch basins below the precious metal baths are also not emptied into the wastewater system but are sealed tight with a ball valve. The catch basins can take the entire content of a bath.
Close Loop Plant Acidic and Alkaline
The different rinse waters are separated into acids and alkalines and kept in individual water cycles where they are permanently cleaned using ion exchangers and carbon filters. Should there be operational problems in these close loop systems during the cleaning process, we can conduct additional separations of the rinse water using separate ion exchangers and carbon filters. The regeneration of the loop plant generates eluates, which are fed into a vacuum evaporator. Wastewater from processes, baths containing used non-precious metals and baths stripped of precious metals are separated into acidic, acidic fluoric, alkaline, and alkaline cyanide wastewater, depending on their composition. Alkaline wastewater containing cyanide is detoxed using oxidation before treated further.
Alkaline and acidic wastewater is mixed to set its pH-level and can be precipitated with caustic soda/sulfuric acid and flocculants, as necessary. The sludge is separated using an automated filter press. Then, the processed wastewater is concentrated in a vacuum evaporator. The filter sludge and evaporation concentrate are disposed of professionally. The remaining distillate is put back into the closed loop plant, so that there is no unnecessary water wastage. Water only leaves the plating process as evaporator concentrate.
Wastewater-Free Production
Water is one of the most valuable resources on our planet. We are driven by our commitment to protect these resources and make them economically sustainable. This is why we strive to operate using wastewater-free plating processes, which allow us to retain all the water in processing cycles thanks to our state-of-the-art treatment methods.
Exhaust Air System
Aerosols — acidic and alkaline — are extracted using two exhaust air pipes. Any rinse water in the exhaust air is fed into the wastewater system. The electrolysis current is disconnected by our plant’s software control, should the exhaust air system fail.
Questions or Sample Requests?
We look forward to your call or message!
Would you like to get to know our products? We would also be happy to send you product samples.
You are currently seeing a placeholder content of HubSpot. To access the actual content, click on the button below. Please note that data will be passed on to third-party providers.
More information